The Ultimate Guide to Ruthenium Iridium Titanium Anodes
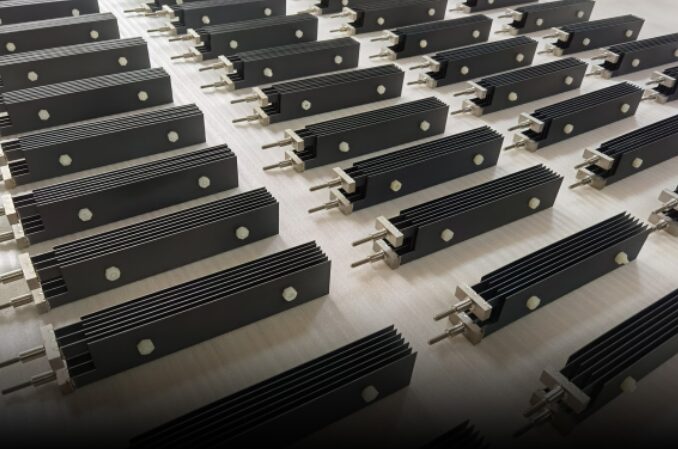
In the modern electrochemical industry, the performance of electrode materials plays a decisive role in the efficiency, energy consumption and product quality of the entire electrochemical process. Ruthenium-iridium-titanium anode, as a high-performance electrode material, has gradually emerged since the late 1960s with the development of dimensionally stable anodes (DSA). Due to its unique performance advantages, it has been widely used in many fields. Wstitanium has also promoted technological progress in related industries. It is based on titanium and coated with precious metal oxides such as ruthenium (Ru) and iridium (Ir). It cleverly combines the characteristics of the three metals and exhibits excellent performance in electrochemical reactions such as chlorine evolution and oxygen evolution, meeting the stringent requirements of different industries for electrode materials.
Advantages of ruthenium-iridium-titanium anode
High electrocatalytic activity : The presence of ruthenium significantly improves the electrocatalytic activity of the anode and can accelerate the electrode reaction rate. In the electrolysis process of the chlor-alkali industry, ruthenium-iridium-titanium anode can make the generation reaction of chlorine and sodium hydroxide proceed more rapidly, greatly improving production efficiency compared with traditional electrode materials. In some organic synthesis processes that require rapid electrochemical reactions, such as the production of glyoxylic acid and succinic acid, ruthenium iridium titanium anodes can also promote the smooth progress of reactions and increase the rate of product generation with their high electrocatalytic activity.
Low overpotential: The anode can significantly reduce the overpotential of chlorine and oxygen evolution reactions. Taking the chlor-alkali industry as an example, the energy consumption required to produce a unit product is significantly reduced after using ruthenium iridium titanium anodes. This is because a lower overpotential means that during the electrolysis process, a smaller voltage can be applied to drive the reaction, thereby reducing the consumption of electrical energy. In the process of preparing hydrogen and oxygen by electrolysis of seawater, the low overpotential characteristic can also reduce the energy consumption required for electrolysis and improve energy efficiency.
Excellent corrosion resistance
Adaptability to complex chemical environments: Whether it is a strongly acidic sulfuric acid solution, an alkaline sodium hydroxide solution, or a salty seawater environment, the ruthenium iridium titanium anode can operate stably for a long time. In the electroplating industry, the anode needs to be immersed in the electroplating solution containing various strong acids and alkalis for a long time. The ruthenium iridium titanium anode can work stably in such an environment with its excellent corrosion resistance, and is not easily corroded and lost, ensuring the continuous and stable progress of the electroplating process. In the field of wastewater treatment, the composition of wastewater is complex and may contain various corrosive substances. The ruthenium iridium titanium anode can also adapt to this complex environment and play its role effectively.
Extend the service life of equipment: Good corrosion resistance prevents the ruthenium iridium titanium anode from being rapidly lost due to corrosion during long-term use, which greatly reduces the maintenance cost of the equipment and extends the service life of the equipment. In the offshore platform facilities of the oil and gas industry, the ruthenium iridium titanium anode used for corrosion protection can work stably for a long time in the harsh marine environment, reducing the trouble and cost of frequent anode replacement, and ensuring the normal operation of offshore facilities.
Dimensional stability
Ensure stable operation: During the electrolysis process, the size of the ruthenium iridium titanium anode can remain stable and the electrode spacing will not change. This feature is crucial for some electrolysis processes that have strict requirements on the electrode spacing. It can ensure uniform current distribution during electrolysis, thereby ensuring the stability of operation and reducing problems such as fluctuations in electrolysis efficiency caused by changes in electrode spacing. In the process of metal electrolysis, stable electrode spacing helps to ensure uniform deposition of metal ions at the cathode and improve the quality of metal products.
Reduce energy consumption: Stable size can reduce additional energy consumption caused by problems such as electrode deformation. If the electrode deforms during the electrolysis process, it may cause uneven current distribution, thereby reducing the efficiency of the electrolysis reaction in some areas. In order to maintain production, more electricity is required. The dimensional stability of the ruthenium iridium titanium anode avoids this situation and helps reduce overall energy consumption.
Low power consumption
Improve overall efficiency: Compared with traditional electrode materials, the ruthenium iridium titanium anode has a low operating voltage and low power consumption. This not only reduces production costs, but also improves the energy efficiency of the entire electrochemical process. In large-scale chlor-alkali industrial production, the amount of electricity consumed every day is huge. The use of ruthenium-iridium-titanium anodes can significantly reduce power consumption and save a lot of electricity expenses for enterprises. At the same time, it also meets the current social requirements for energy conservation and emission reduction, and helps to promote the industry to develop in a green and efficient direction.
·
Manufacturing of ruthenium-iridium-titanium anodes
Pretreatment of titanium substrate
Surface cleaning: The titanium substrate needs to be strictly cleaned before coating. First, sandblasting is used to impact the surface of the titanium substrate with high-speed jet abrasives (such as silicon carbide, etc.) to remove oil, oxide scale and other impurities on the surface, and at the same time, a certain degree of roughness is formed on the surface to increase the adhesion between the coating and the substrate. Then the titanium substrate is placed in deionized water for ultrasonic cleaning to further remove the fine impurities remaining on the surface and ensure the cleanliness of the substrate surface.
Hot-setting and pickling: The titanium substrate that has been cleaned on the surface is subjected to hot-setting treatment to eliminate the internal stress generated during the processing and ensure the dimensional accuracy and shape stability of the titanium substrate. Then pickling is carried out, and the titanium substrate is immersed in a pickling solution prepared by oxalic acid, hydrochloric acid, etc., to further remove metal impurities and oxide films on the surface, so that the surface of the titanium substrate is exposed to a fresh metal surface, providing a good foundation for subsequent coating. The concentration and immersion time of the pickling solution need to be precisely controlled according to the actual situation. Generally, the concentration of the pickling solution is about 16.78wt%, and the immersion time is 40-50min. After the pickling is completed, the acid solution on the surface of the titanium substrate is blown dry with a waterless air dryer before proceeding to the next step.
Coating preparation
Solution preparation: Prepare base metal solution and precious metal solution separately. Taking the preparation of ruthenium, iridium, tin and titanium coated titanium anode as an example, when preparing the base metal solution, first add a certain amount of tin source into an appropriate amount of methanol solution, dissolve it under stirring to obtain a transparent solution; then add polyethylene glycol 600 into the transparent solution to obtain a transparent solution; then add sodium hydroxide into the transparent solution to obtain a milky white solution; after stirring the milky white solution for 3-10 minutes, transfer it to a high temperature and high pressure reactor, keep it at 170℃-190℃ for 10-12h, and then cool it at room temperature to obtain a precursor solution; wash the precursor solution repeatedly with deionized water for several times, and use silver nitrate solution to check the chloride ions in the suspension during the washing process until there are no chloride ions in the suspension, and the washing is completed to obtain the precursor; centrifuge the precursor and dry it at 80℃-120℃ for 2-3 hours. 5h, nano-scale tin dioxide powder can be obtained; finally, the prepared nano-scale tin dioxide powder is dispersed in an organic solvent (such as one or more of ethylene glycol, n-butanol, isopropanol, and anhydrous ethanol) to obtain a base metal solution.
Preparation of precious metal solution: Weigh the ruthenium source and iridium source and dissolve them in an organic solvent. Under the combined action of mechanical stirring and ultrasound, the ruthenium source and iridium source are completely dissolved to obtain a solution; a mixed solution of citric acid and alcohol solution is added to the obtained solution, and a solution is obtained under the combined action of mechanical stirring and ultrasound; then butyl titanate is added to the solution, and a precious metal solution is obtained under the combined action of mechanical stirring and ultrasound.
Mixing and coating: The prepared base metal solution and the precious metal solution are fully mixed to obtain a mixed solution. Then the mixed solution is coated on the pretreated titanium substrate. There are many coating methods, the most common of which are brush coating and spray coating. The brushing method is to use a soft brush to evenly apply the mixed solution on the titanium substrate. This method is simple to operate, but the efficiency is low. It is suitable for small-batch production or occasions with high coating precision requirements; the spraying method is to use a spray gun to atomize the mixed solution and spray it onto the surface of the titanium substrate. This method is more efficient and has better coating uniformity, which is suitable for large-scale production. The coated titanium substrate is dried at 60-120℃ for 5-15 min, and the dried titanium electrode is sintered at 450-550℃ for 10-20 min.
Multiple cycles and final sintering : Repeat the coating, drying, and sintering process until the prepared mixed solution is completely coated on the titanium substrate. Finally, the ruthenium-iridium-titanium coated titanium anode is obtained by heat preservation and sintering at 450℃-550℃ for 0.5h-2h. Through multiple cycles of coating and sintering, the coating can be made more uniform and dense, and the performance of the anode can be improved.
Automated production
In order to improve production efficiency, reduce labor costs and ensure the stability of product quality, some automated production equipment for titanium-based ruthenium-iridium coated anode materials has also appeared. This equipment includes an active pay-off frame, a small tension wire storage frame that matches the active pay-off frame, a sandblaster, a heated pickling tank, an anhydrous air dryer 1, a water washing tank, an anhydrous air dryer 2, a dryer, a parallel wire wheel, a traction machine front end, an automatic brush applicator, a peristaltic pump loaded with saturated solution, an oven, a pipeline sintering furnace, a traction machine rear end, a meter, a take-up frame, a control cabinet with a PLC controller, an automatic coiling machine and an air compressor. Starting from the pay-off of the titanium wire, it goes through a series of processes such as surface treatment, pickling, water washing, drying, brushing, baking, sintering, etc., and finally completes the preparation of the titanium-based ruthenium-iridium coated anode material. The entire process is automatically controlled, reducing manual intervention and improving the accuracy and consistency of production.
Application of Ruthenium Iridium Titanium Anode
Chlor-alkali Industry
Chlor-alkali industry is one of the important application fields of Ruthenium Iridium Titanium Anode, which is mainly used to produce caustic soda (sodium hydroxide) and sodium hypochlorite and other products. In the chlor-alkali electrolysis process, saturated salt water is used as raw material, and chlorine is generated at the anode through electrolysis reaction, and hydrogen and sodium hydroxide are generated at the cathode. With its high electrocatalytic activity and low overpotential, Ruthenium Iridium Titanium Anode can efficiently promote the generation reaction of chlorine, reduce the energy consumption of the electrolysis process, and improve production efficiency. At the same time, its excellent corrosion resistance can also ensure long-term stable operation in electrolytes containing high concentrations of chloride ions and strong alkalinity, reduce electrode loss and replacement frequency, and reduce production costs.
Swimming pool disinfection : Using the chlorine-release performance of ruthenium iridium titanium anode, the sodium chloride put into the swimming pool is electrolyzed to generate sodium hypochlorite. Sodium hypochlorite has strong oxidizing properties and can kill bacteria and viruses in the water to achieve swimming pool water disinfection. Compared with traditional chemical disinfection, this disinfection method is more environmentally friendly and safe, does not produce harmful by-products, and can also reduce corrosion to swimming pool equipment.
Sewage treatment: In the field of sewage treatment, ruthenium iridium titanium anode can be used to treat various industrial wastewaters and domestic sewage. Through electrochemical oxidation, the organic pollutants in the sewage are decomposed, the chemical oxygen demand (COD) and biochemical oxygen demand (BOD) are reduced, and the sewage meets the discharge standards. For some industrial wastewaters containing difficult-to-degrade organic matter, such as printing and dyeing wastewater, pharmaceutical wastewater, etc., the electrochemical treatment method of ruthenium iridium titanium anode can achieve better treatment effects, providing an effective technical means for sewage treatment.
Hydrogen and oxygen production : Ruthenium-iridium-titanium anodes have important applications in the process of preparing hydrogen and oxygen by electrolysis of seawater. Due to the complex composition of seawater, which contains a large amount of salt and other impurities, the corrosion resistance of electrode materials is extremely high. Ruthenium-iridium-titanium anodes can work stably in such harsh environments, efficiently catalyze the electrolysis of water, and achieve the production of hydrogen and oxygen. As a sustainable way to produce hydrogen, seawater electrolysis is of great significance for solving energy problems, and the application of ruthenium-iridium-titanium anodes provides key technical support for it.
Problems with ruthenium-iridium-titanium anodes
High cost of precious metals : Ruthenium and iridium are precious metals and are expensive. In the preparation process of ruthenium-iridium-titanium anodes, a certain amount of ruthenium and iridium are required, which makes the production cost of anodes high. Especially with the fluctuation of precious metal market prices, the cost of ruthenium-iridium-titanium anodes will also be greatly affected, increasing the procurement cost and production cost pressure of enterprises, and limiting their wide application in some cost-sensitive fields.
High preparation cost: In addition to the cost of the precious metal itself, the preparation process of ruthenium iridium titanium anode is relatively complicated and requires multiple processes, such as pretreatment of the titanium substrate, preparation of the coating solution, coating and sintering, which also increases the preparation cost. Moreover, during the preparation process, the requirements for equipment and process are high, which further increases the cost threshold of production.
Stability problem
Degradation of performance in long-term use: Although the ruthenium iridium titanium anode has good stability, in the long-term use process, due to the influence of factors such as complex electrochemical environment and mechanical stress, its coating may wear and fall off, resulting in a gradual decline in the performance of the anode. In some high-temperature and high-current density electrolytic environments, this stability problem is more prominent, affecting the service life of the anode and the stability of the electrolytic process.
Sensitive to environmental factors: The performance of the ruthenium iridium titanium anode is sensitive to environmental factors, such as the composition, temperature, pH, etc. of the electrolyte. When the environmental factors change significantly, the corrosion rate of the anode may be accelerated and the electrocatalytic activity may be reduced, thereby affecting the normal operation of the anode. In practical applications, it is difficult to completely ensure the constancy of environmental factors, which also brings certain challenges to the stable operation of ruthenium iridium titanium anodes.
Recycling issues
Difficulty in recycling: After the ruthenium iridium titanium anode is scrapped, its recycling process is relatively complicated. The anode needs to be disassembled from the equipment and physically cleaned, and then the alloy layer is dissolved by acid or other solvents at high temperature, and finally ruthenium and iridium are separated from other impurities by electrolysis or chemical methods in the refining stage. The entire recycling process requires professional equipment and technology, and some harmful waste gas and wastewater may be generated during the dissolution and refining process, causing certain pollution to the environment.
Low recycling efficiency: At present, the recycling technology of ruthenium iridium titanium anodes is not mature enough, and the recycling efficiency is low, resulting in the inability to effectively recycle some precious metals, resulting in a waste of resources. In addition, the high recycling cost makes some companies less enthusiastic about the recycling of ruthenium iridium titanium anodes, which is not conducive to the recycling and sustainable development of resources.
Summary
As a high-performance electrode material, ruthenium-iridium-titanium anode plays an important role in many fields such as chlor-alkali industry, water treatment, seawater electrolysis, water heater anti-corrosion, metal electrolysis, organic electrolysis, etc., with its excellent electrochemical properties, outstanding corrosion resistance, dimensional stability and low power consumption, and has promoted the technological progress and development of related industries. However, it also has problems such as high cost, stability needs to be further improved, and recycling is difficult. In the future, it is necessary to explore ways to reduce costs through technological innovation, such as developing new coating materials or optimizing preparation processes to reduce the use of precious metals; on the other hand, further improve the stability and durability of the anode, and study more effective surface treatment technologies and protective measures; at the same time, strengthen the research on the recycling technology of ruthenium-iridium-titanium anodes, improve recycling efficiency, reduce recycling costs, and realize the recycling of resources. It is believed that with the continuous development and improvement of technology, ruthenium-iridium-titanium anodes will show a broader application prospect in the field of electrochemistry and make greater contributions to industrial production and social development.
Source: The Ultimate Guide to Ruthenium Iridium Titanium Anodes